Field of application
Welding is a broad topic, by field of application, by type of material, by process. We wire weld structural steel (S235JR, S355J2, S420MC, S700MC, S900MC) and tempered material (C40, C45,39NiCrMo3, 42CrMo4) . Our typical thicknesses of medium-light carpentry, i.e. between 3 and 20 mm.
For these applications we are ISO3834-3 certified and in this short article we try to illustrate the key points borrowed from our experience, a list of smart tips.
Difference between MiG and MAG process
Our welds are all MAG welds, which means that the welding gas is active, i.e. it comes into play in the process. MIG welding, on the other hand, uses an inert gas (usually helium or argon); in this case the gas only “protects” the welding, i.e. it does not take part in the fusion reaction. The machine is always the same, MAG welding is used for carbon steels, instead MIG for stainless steels.
Welding process variables:
Material
It is essential to know the nature of the material we have to weld, quality and thickness. Finally, pickled material is preferable both for a better aesthetic result and to avoid incorporating impurities in the joint.
Gas
The gas for our welding technique is an active gas as a mixture of Argon (Ar) and Carbon Dioxide (CO₂). The percentage of CO₂ (which is the active gas) affects the execution of the welding.
When CO₂ increases we have:
- Greater penetration
- Greater heat input on the piece
- Better arc stability
- Basically more dots
- A less aesthetic seam
The most common blends have a CO₂ percentage of 8%, 13%, 18% and 25%.
For welding with pulsed arc it is necessary to use only mixtures with a percentage of no less than 15%.
The gas is stored at high pressure in the liquid state which also means at low temperatures, therefore it would be good practice to have a pre-heating system at the cylinder outlet before distribution in the network towards the welders.
Finally, in recent years, mixtures enriched with Nitrogen or Helium are gaining ground. Despite the commercial intent, according to our experience, these blends are truly effective only in particular application cases, i.e. the benefits do not justify the higher costs.
Wire
The choice of wire can make all the difference in the wire welding process.
Surely there are wires which, although falling within the same ISO/AWS class, still have better performance than others, even if with different costs. The current commercial offer is truly vast and you have to rely on professionals in the sector.
However, the mechanical resistance that the wire can guarantee must certainly be verified. For example, for the most common solid (non-cored) wires for carbon steel, it can be deduced from the pair of numbers following the letter G inside the abbreviation (not to be confused with the abbreviations SG). Indicates the yield strength, for example a G46 has a yield strength of 460N/mm². Finally, to be considered a good wire for medium-light welding, it must fall into the SG2 category.
Welding machine
The offer of welding machines is wide and you will find detailed explanations on the various manufacturers’ websites. Surely a quality generator (unfortunately even more expensive) greatly helps the stability of the arc and therefore the effectiveness of the joint.
Let’s just remember that an inverter welding machine by itself does not improve the arc but saves electricity.
The synergic function, on the other hand, allows the machine to self-regulate (again it is effective if the welding machine is equipped with good electronics).
Pulsed arc has the advantage of less dirt (fewer pellets) and for a poorly educated hand it could help to obtain a more aesthetic cord. However, care must be taken because with the same current values, the pulsed arc heats up more (therefore potentially greater shrinkage problems) and penetrates the material less.
The welding machines used within the ISO 3834 certification must in turn be certified
Current intensity
The amperage with which a MAG wire welding is performed conditions the actual deposition process.
Considering for example a 1 mm diameter G46 SG2 wire, with a stick out distance of 12-15mm, we obtain:
- Short arc deposit for currents between approximately 50 and 160 Ampere.
- Globular deposit for currents between approximately 160 and 200 Ampere.
- Spray arc depot for currents above approximately 200 Ampere.
Surely the best and cleanest execution is in spray arc, so where possible it is suggested to maintain a high current. The current value affects the electric arc that is established and consequently the way in which the wire melts and is deposited.
We recommend the following video:
Joint type
There are different types of joints, the most common being butt-to-butt or angled. The welding technique must be adapted to the shape of the joint itself in order to safeguard all the other parameters for excellent welding (piece position, torch position, execution speed, etc.)
Preparation of material
It depends on the type of joint to be made. Surely it is good practice to always break the sharp edge of the material by rounding it off with a flexible hose.
For structural welding, on the other hand, it is necessary to prepare the material with chamfers (also called chamfers), the presence of the chamfer facilitates subsequent penetration.
Torch position
It is a fundamental fact that the torch assumes the most suitable position possible. Compared to an ideal frontal section, it should be positioned along the axis of the bisector. While longitudinally to the cord it should assume an inclined position of 15°-30°.
The distance from the piece varies according to the technique but for a globular welding, the distance is about 12-15mm, which also corresponds to the protrusion of the wire from the stick out torch)
Furthermore, as far as possible it is very important that the wire welding is carried out flat. To achieve our goal, there are different types of torches on the market with different shapes and inclinations.
Therefore, following the position described above, the welding should be performed in push and not pull. In practice it happens that sometimes it is possible to perform a better weld if tight, for example near corners in order to prefer a regular flow of gas.
Mass clamp position
Not always considered, but the position of the mass clamp also plays a fundamental role in limiting current dispersion and therefore maintaining a more stable arc (as well as saving energy). Therefore it is a good rule to attach the mass directly to the piece and only if it is not possible to the work table, but still as close as possible to the piece.
Welding quality inspection
The verification of the goodness of a weld joint takes place through non-destructive tests performed by qualified personnel (at least at level 2). Among these controls are:
- Visual (VT)
- liquid penetrant (PT) or electromagnetic yoke (MT)
- Ultrasound (UT) or radiographic (RT) control
The first two are surface checks while the UT and RT checks are defined as volumetric checks because they are able to analyze the joint even in depth.
On the other hand, to verify the process it is also possible to carry out destructive tests, thus being able to carry out macrography, micrography and hardness on the bead as well as mechanical tests. They are tests to be performed in the laboratory.
Welding of tempered steels
To weld hardened and tempered steels (e.g. C40, C45, 39NiCrMo3, 42CrMo4) the material must first be preheated. The preheating level depends on the type of material and the size of the piece, however in the order of 150°C – 200°C. Verification of the temperature can be done with thermal chalks.
Finally, the phase after welding is equally important, which requires controlled and “slowed” cooling in order to avoid the formation of micro cracks. For this reason it is customary to cool the pieces in sand (use of vermiculite) instead of in the air.
ISO 3834 certification
It is a standard that certifies the company’s welding process. It does not directly certify the single piece as, for example, happens with ISO 1090.
The standards already present in the more widespread ISO9001 are largely referred to, then specifically it guarantees the traceability of the materials used (semi-finished products, consumables, etc.), the training of personnel, the effectiveness of the instruments and machinery, the parameters execution of the welds and its control. This is why certified companies almost always have visual inspection (VT) and non-destructive testing (PT, penetrant liquids and electromagnetic yoke) authorized personnel
ISO 3834 certification provides for 3 sub-levels based on the type of product and therefore on the level of monitoring necessary for the production cycle. The levels are: 4: basic, 3: medium, 2: advanced.
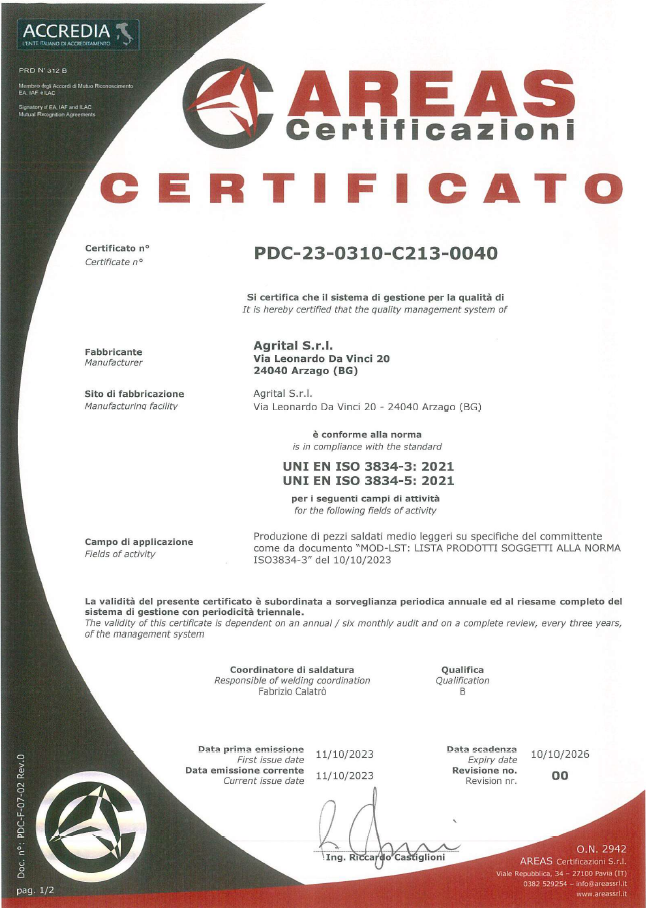
Heat treatments after welding
A brief note on the heat treatments of welded parts. They can represent a strong criticality if not performed scrupulously, so it is good to rely on specialized companies, possibly able to issue certifications on their process and control the piece performed.
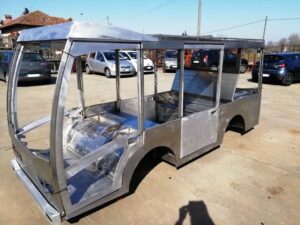
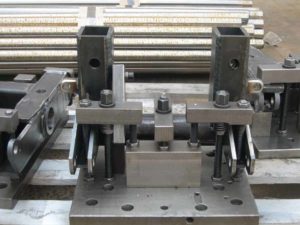
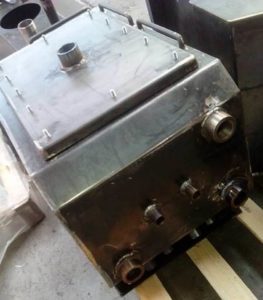
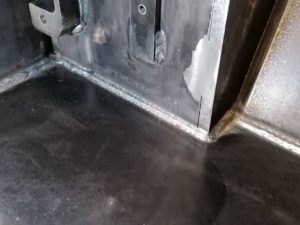
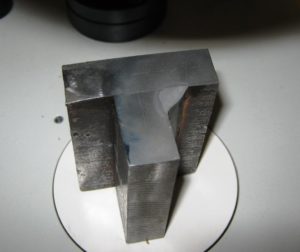
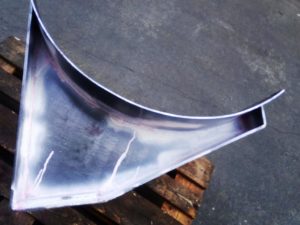
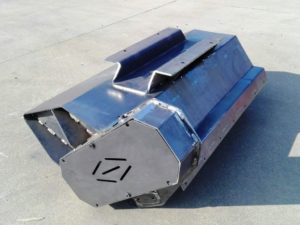
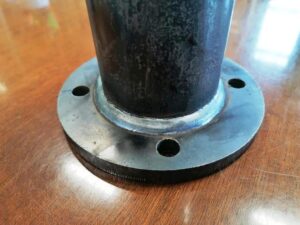
Agrital
We are a metalworking company active since 1972. We started in the agricultural mechanization sector with the construction of tractor cabins.
Today, thanks to a staff of over 50 people, we are present in various product sectors, mainly producing driver’s cabins, hydraulic tanks and hoods (metal casing). In addition to having been the forerunners since 2003 in laser tube processing.